Projelerim
Yüzey Finisaj İstasyonu ve Hareketli Tabla Mekanizması Geliştirme
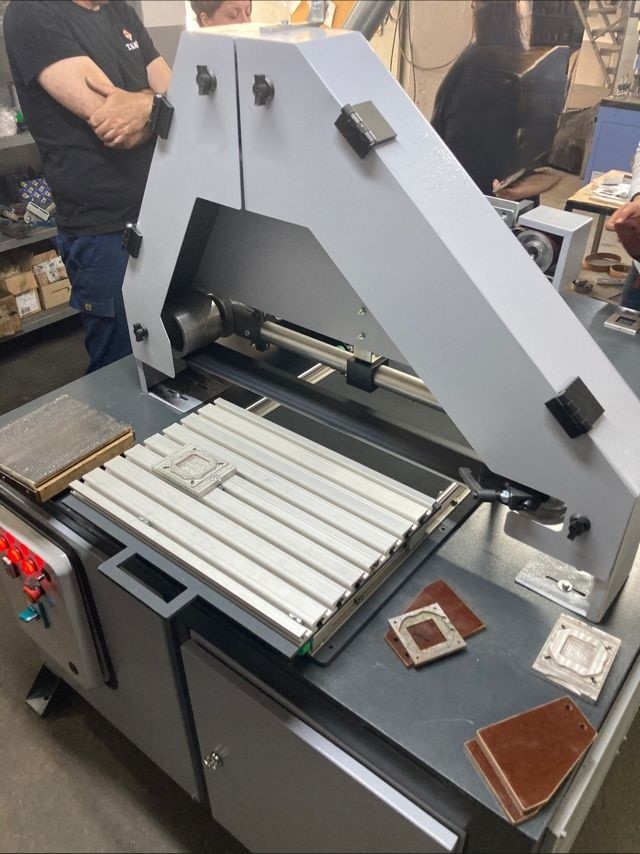
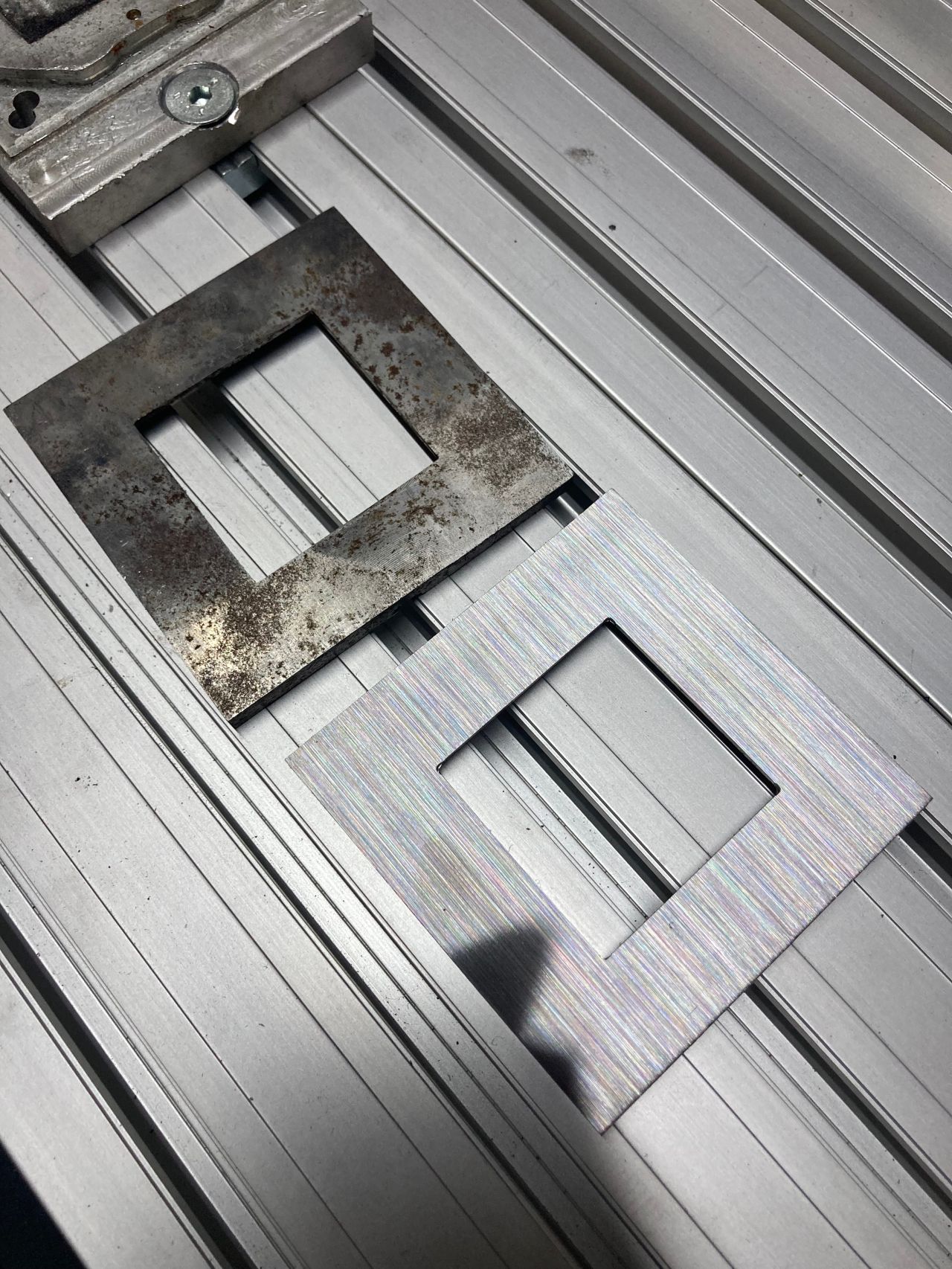
Sistem Bileşenleri
- Üst Gövde Yapısı: Rijitlik ön planda tutularak tasarlandı. İki yandan destekli ve yüksek dayanımlı çelik profillerle kaynaklı konstrüksiyon oluşturuldu.
- İleri-Geri Hareketli Tabla: Yüksek hassasiyetli lineer kızak sistemi (HIWIN marka) kullanıldı. Manuel veya yarı otomatik hareket kabiliyetine sahip.
- İş parçası platformu, slotlu sigma profiller ile çok yönlü ve birden fazla parçayı sabitlemeye olanak verir.
- Finisaj: Motor tahrikli taşlama için sonsuz bant zımpara ve zımpara kasnağı entegre edilmiştir.
- İşlem bölgesi, operatör güvenliği gözetilerek kısmen kapalı alanda çalışır.
Sorumluluklarım
- Tüm sistemin 3B CAD tasarımını gerçekleştirdim (SolidWorks).
- Sipariş edilmesi gereken malzemeler tasarıma ve bütçeye göre seçildi ve sipariş aşaması tarafımca sağlandı.
- İmalat çizimleri, parça listesi, montaj planlaması gibi tüm dökümantasyonu hazırladım.
- Prototip üretim sürecinde birebir yer aldım, üretim sonrası operasyonel testleri yönettim.
Sonuçlar ve Kazanımlar
- Yüzey düzgünlüğü önceki işleme göre gözle görülür şekilde iyileştirildi.
- İşlem süresi manuel yönteme göre yaklaşık %40 oranında kısaldı.
- Sistem, üretim hattına başarıyla entegre edildi ve operatörler tarafından benimsendi.
Boru Dış Yüzey Taşlama ve Finisaj Makinesi
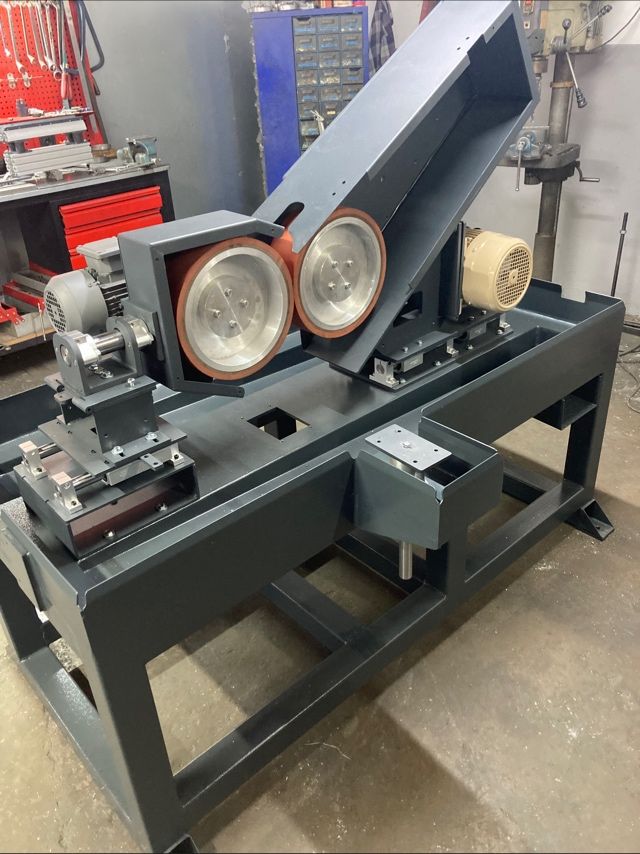
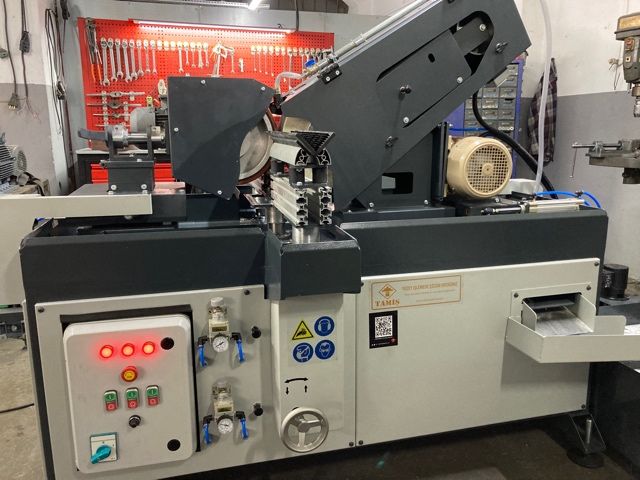
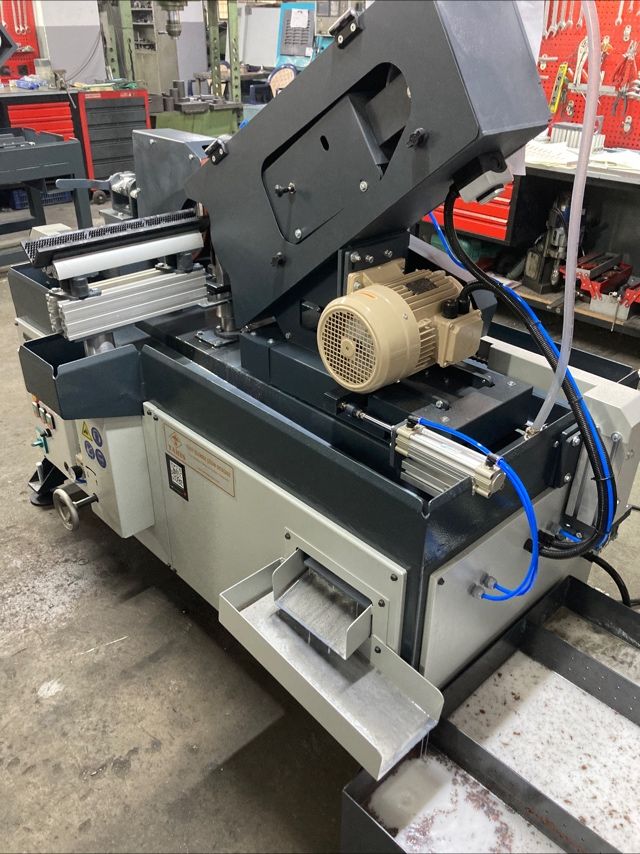
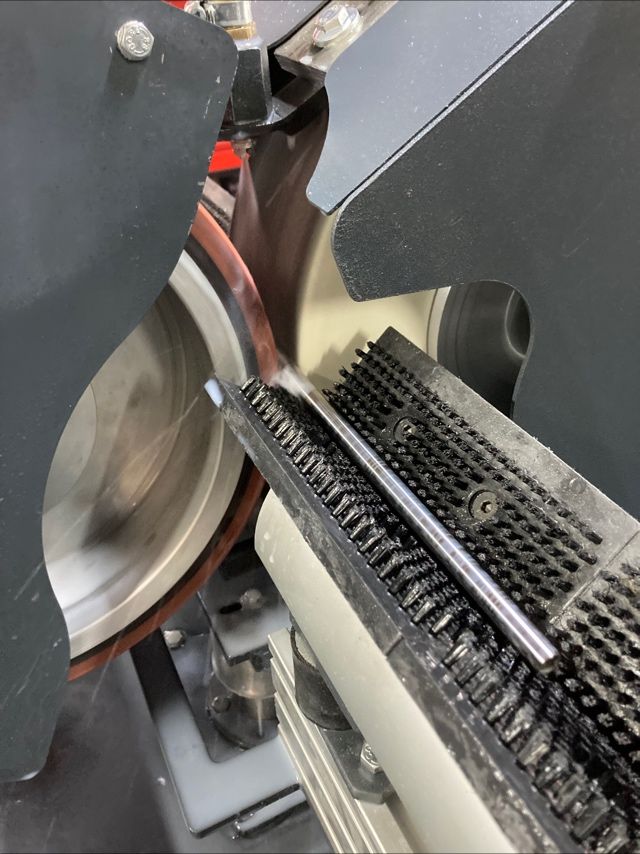
Teknik Özellikler
- Taşlama Başlığı: Ø200 mm çapında iki adet taşlama diski, karşılıklı olarak konumlandırıldı. Disklerin arasında kalan boşluktan boru geçirilerek 360° çevresel taşlama sağlanır. Açı ayarlanabilir yapıdadır.
- Tahrik Mekanizması: Güçlü ve titreşimsiz çalışma sağlayan trifaze motor ile sürülür. Taşlama kuvveti ve yüzey baskısı kullanıcı tarafından ayarlanabilir.
- Taşıyıcı Sistem: Boru, konveyör benzeri fırçalı makaralar üzerinden taşlama ünitesine ilerletilir. Malzeme fırça sistemine temas ederek hem desteklenir hem de dönmesi sağlanır.
- Şasi ve Konstrüksiyon: Yüksek dayanımlı kutu profil şasi üzerinde modüler yapı tercih edilmiştir. Sürgü sistemleri kızaklarla konumlandırılmıştır (lineer raylar ve ayarlanabilir bloklar).
- Kontrol: İşlenen parçanın çapı çarklarla ayarlanır ve numaratörlerde hangi çapta işlem yapılacağı operatör tarafından belirlenir. Pnömatik sistemlerle desteklenen parça tutma ve tahliye birimi entegre edilmiştir.
Sorumluluklarım
- Tüm sistemin mekanik tasarım süreci bana aittir (3D modelleme, imalat çizimleri, parça üretim dosyaları, toleranslandırma).
- Üretim sürecinde işlenebilirlik kontrolü, montaj adımları, test ve devreye alma aşamalarında aktif görev aldım.
- Makineyi modüler yapıda tasarlayarak hem taşlama diski hem de taşıma sistemlerinin farklı çapa göre uyumlandırılabilir olmasını sağladım.
- Pnömatik sistemlerin yerleşimi ve boru ilerleme açısı optimizasyonu konusunda çözüm geliştirdim.
Performans ve Sonuç
- Taşlanan yüzeyin ortalama pürüzlülüğü (Ra) < 1.6 µm düzeyine indirilebildi.
- İşlem süresi, manuel taşlama yöntemlerine göre %60 oranında azaltıldı.
- Operatör açısından güvenli ve ergonomik bir yapı elde edildi.
Almanya İhracatı – Infeeder ve Outfeeder Sistemleri Geliştirme
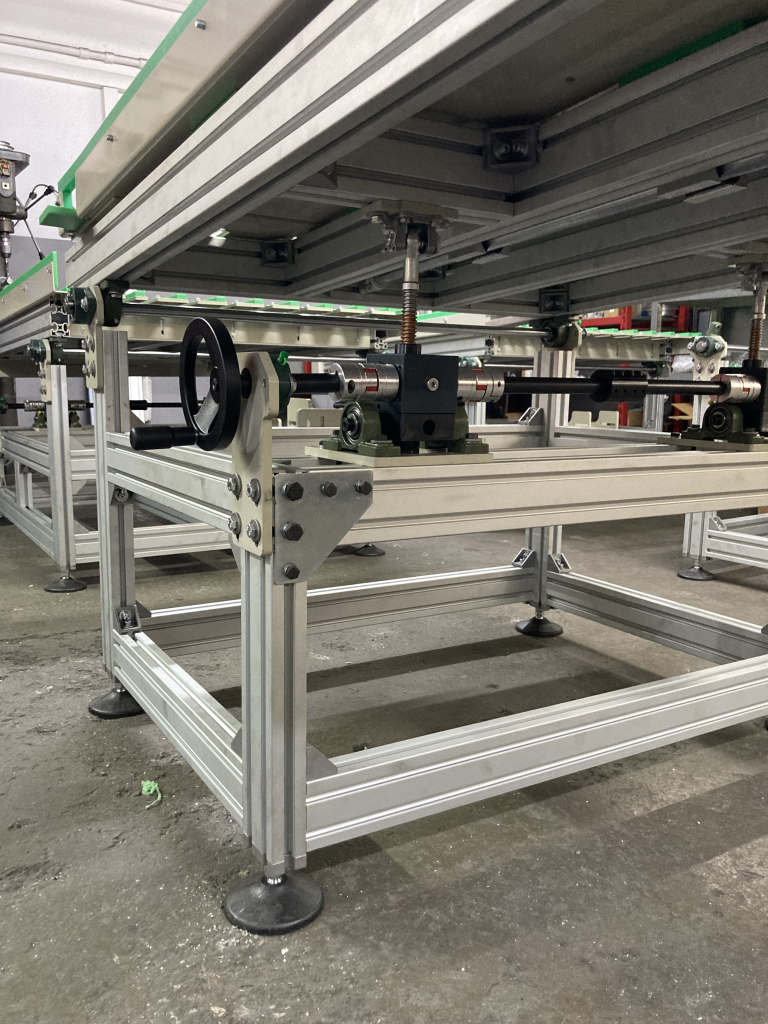
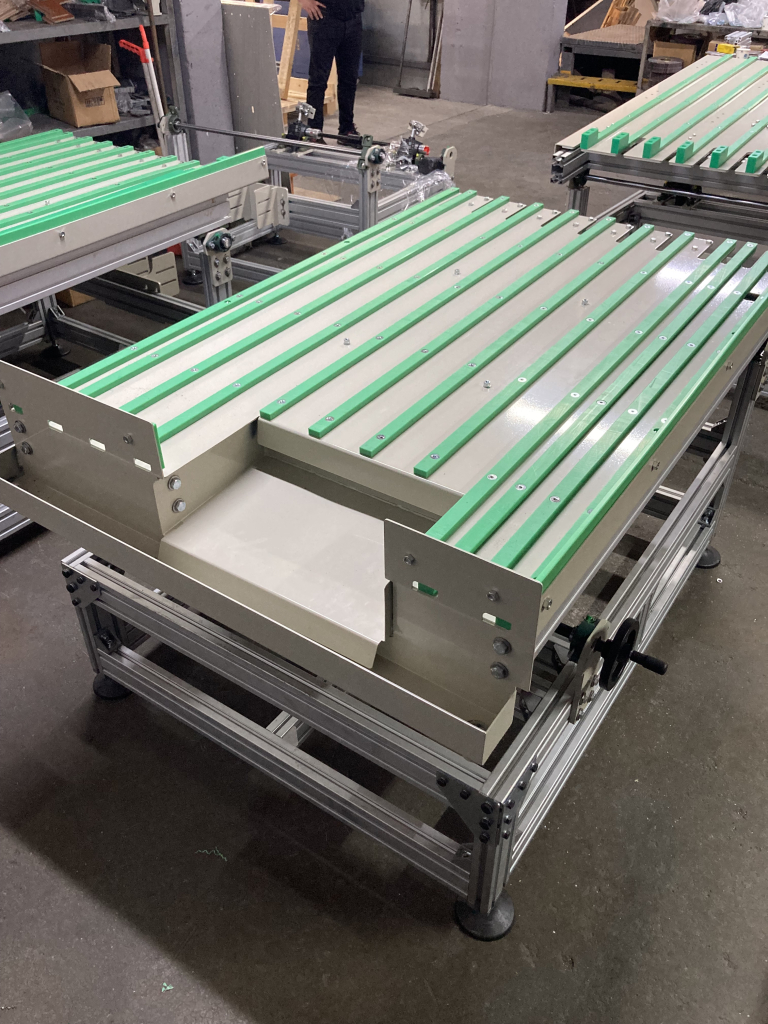
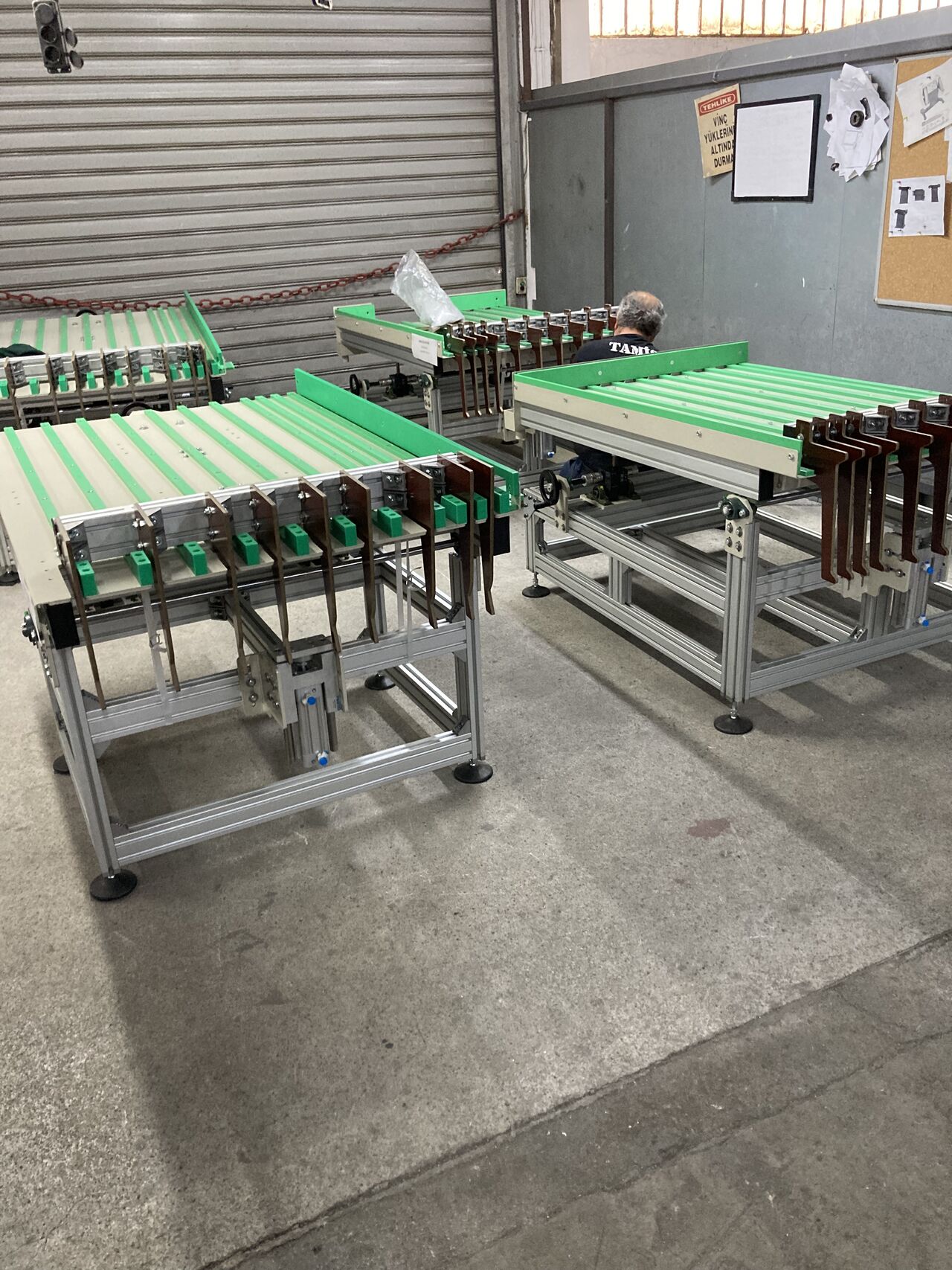
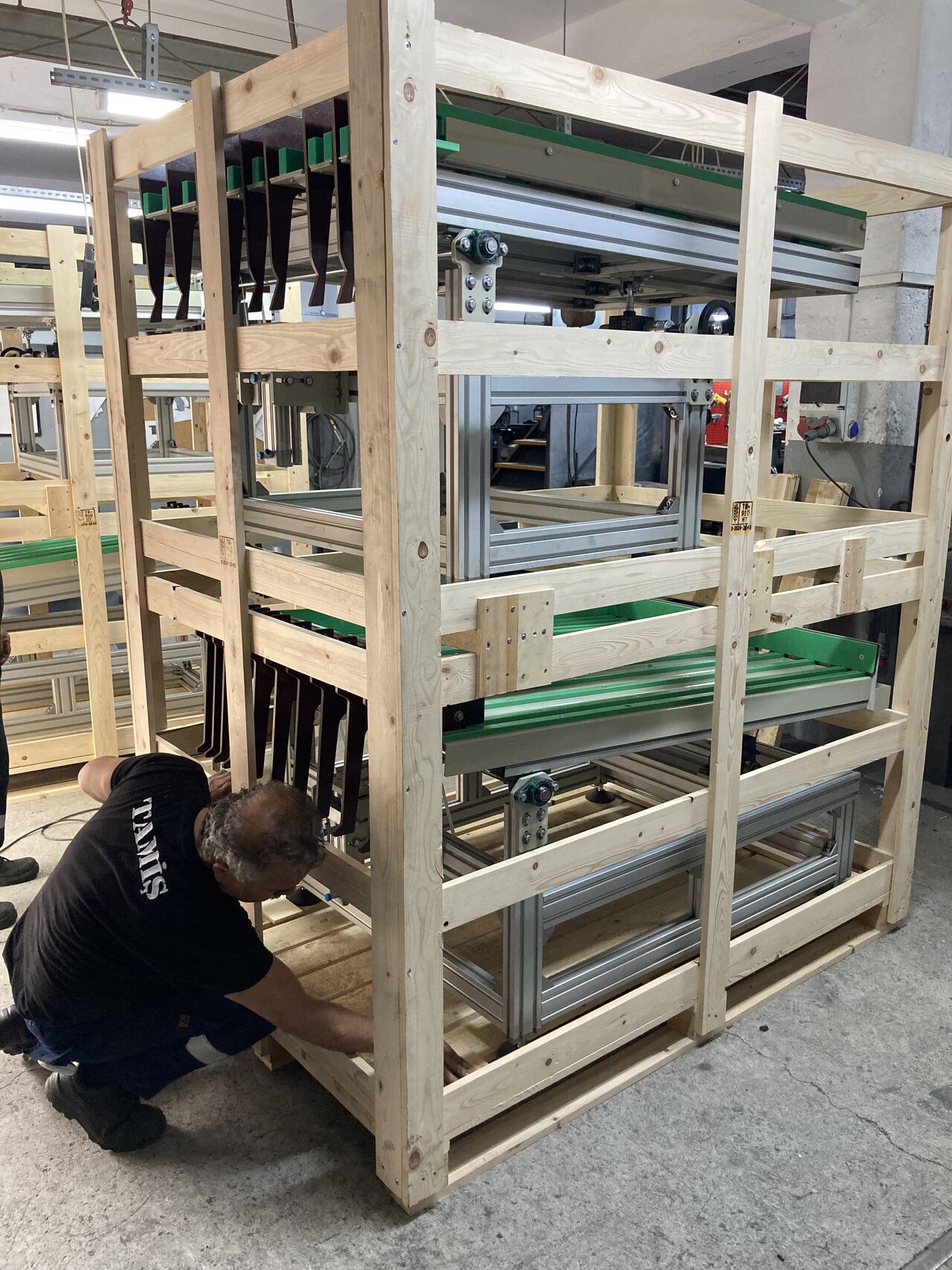
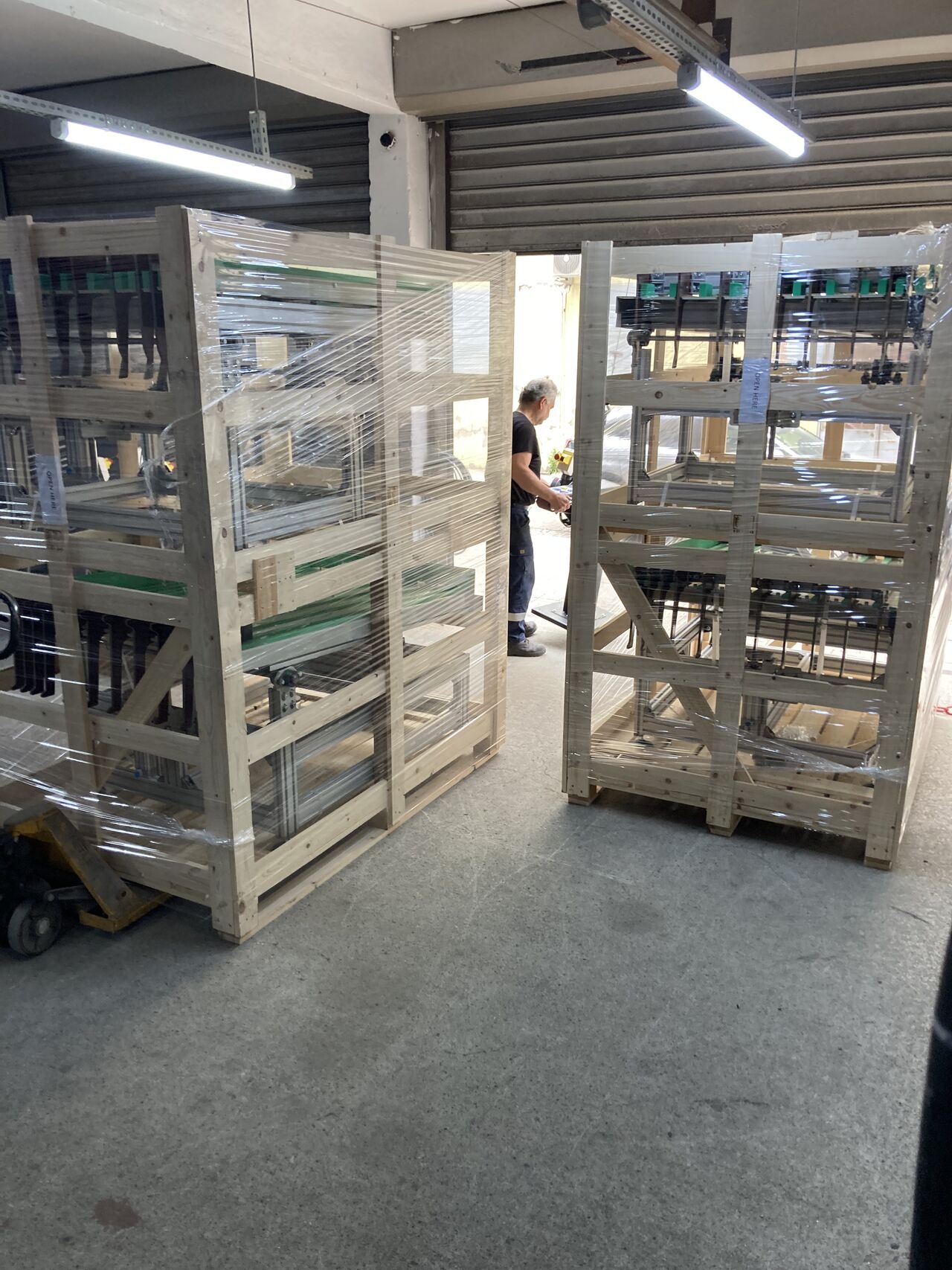
Teknik Özellikler
- Konstrüksiyon: Ana taşıyıcı yapı 40×40 alüminyum profil (DIN EN 12020-2) ile oluşturulmuştur. Ayarlanabilir kauçuk ayaklar, zemin eğimlerine göre hizalama sağlar.
- Taşıma Yüzeyi: Her konveyör ünitesinde, yüksek dayanımlı yeşil PE1000 malzeme kullanılmıştır. Malzeme kaymasını önlemek amacıyla kanal arası optimize edilmiştir.
- Hareket ve Ayar Mekanizması: Manuel tahrikli vida mili ve rulman destekli el volanı sistemi sayesinde konveyör yüksekliği hassas şekilde ayarlanabilir (kriko sistemi). Yan kılavuzlar, farklı ürün boyutlarına göre esnek ayarlama olanağı sunar.
- Taşıma ve Montaj: Tüm sistemler özel çift katlı ahşap sandıklarda ambalajlandı ve ihracata hazır şekilde paletlenip sevk edildi. Paketleme esnasında her ünite parça bazlı kontrol edilerek montaj kılavuzlarıyla birlikte gönderildi.
Sorumluluklarım
- 3D modelleme, teknik resim oluşturma ve montaj planları tarafımdan çizilmiştir.
- Tüm teknik resimler DIN ISO 7200 başlık alanı yapısına ve DIN 406 çizim standartlarına göre hazırlanmıştır.
- Toleranslar, yüzey pürüzlülükleri ve montaj arayüzleri Alman üretim ekiplerinin anlayabileceği evrensel çizim diliyle belirtilmiştir.
- Üretim sürecinde kalite kontrol, iş parçası denemeleri uygun açı ve ölçüler benim tarafımdan denetlenmiştir.
Sonuç ve Katma Değer
- Sistemler karşı firmanın üretim hattına birebir entegre edilecek şekilde sıfır hata ile teslim edildi.
- Kurulum sonrası ölçü uyumsuzluğu yaşanmadı.
- El ile yapılacak malzeme aktarım süresi yaklaşık %35 azaltıldı.
- Tasarımda modülerlik ön planda tutularak sonraki sistemlere kolayca adapte olabilecek yapı sağlandı.
Tam Otomatik Havlupan Taşlama Makinesi
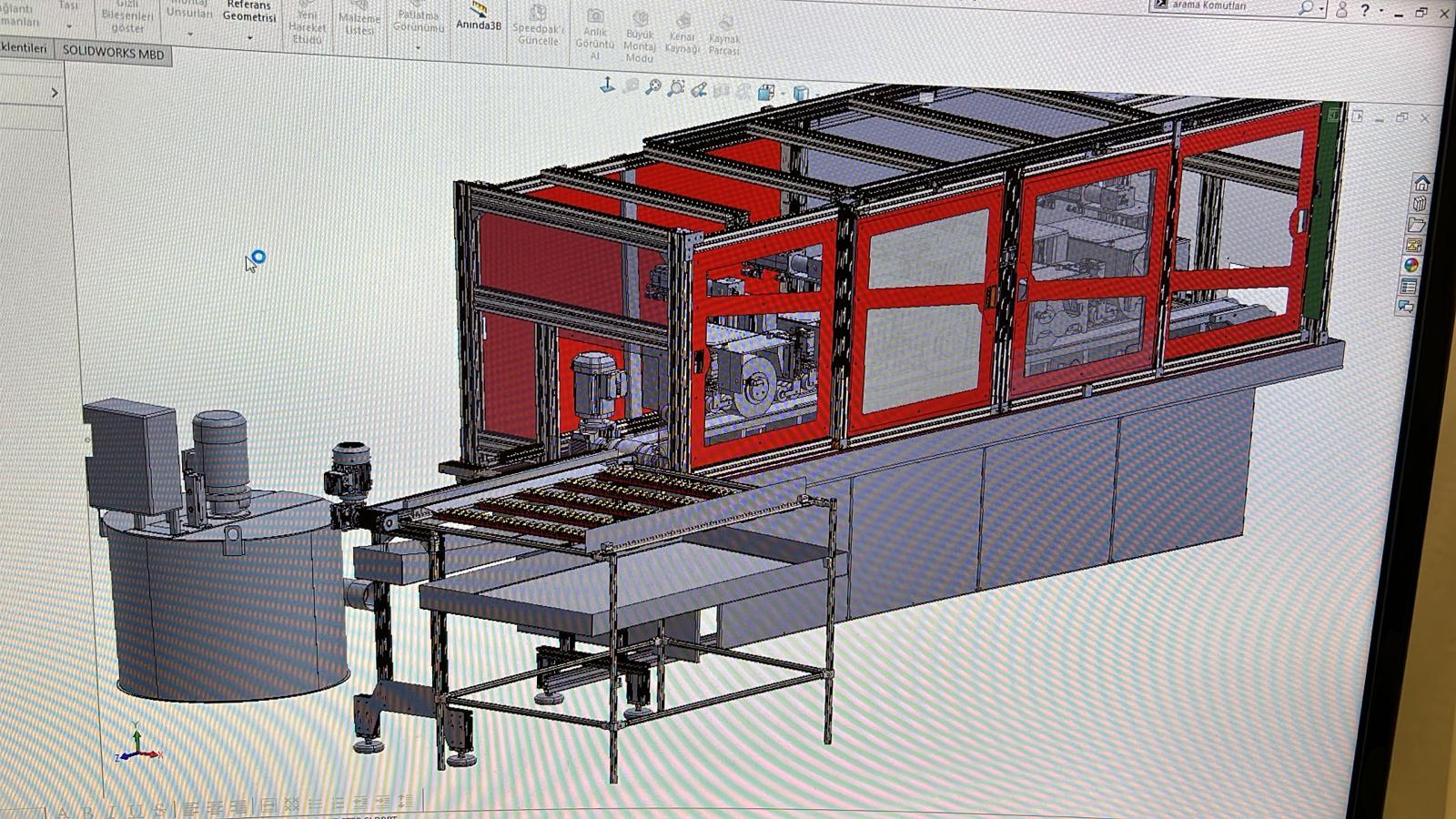
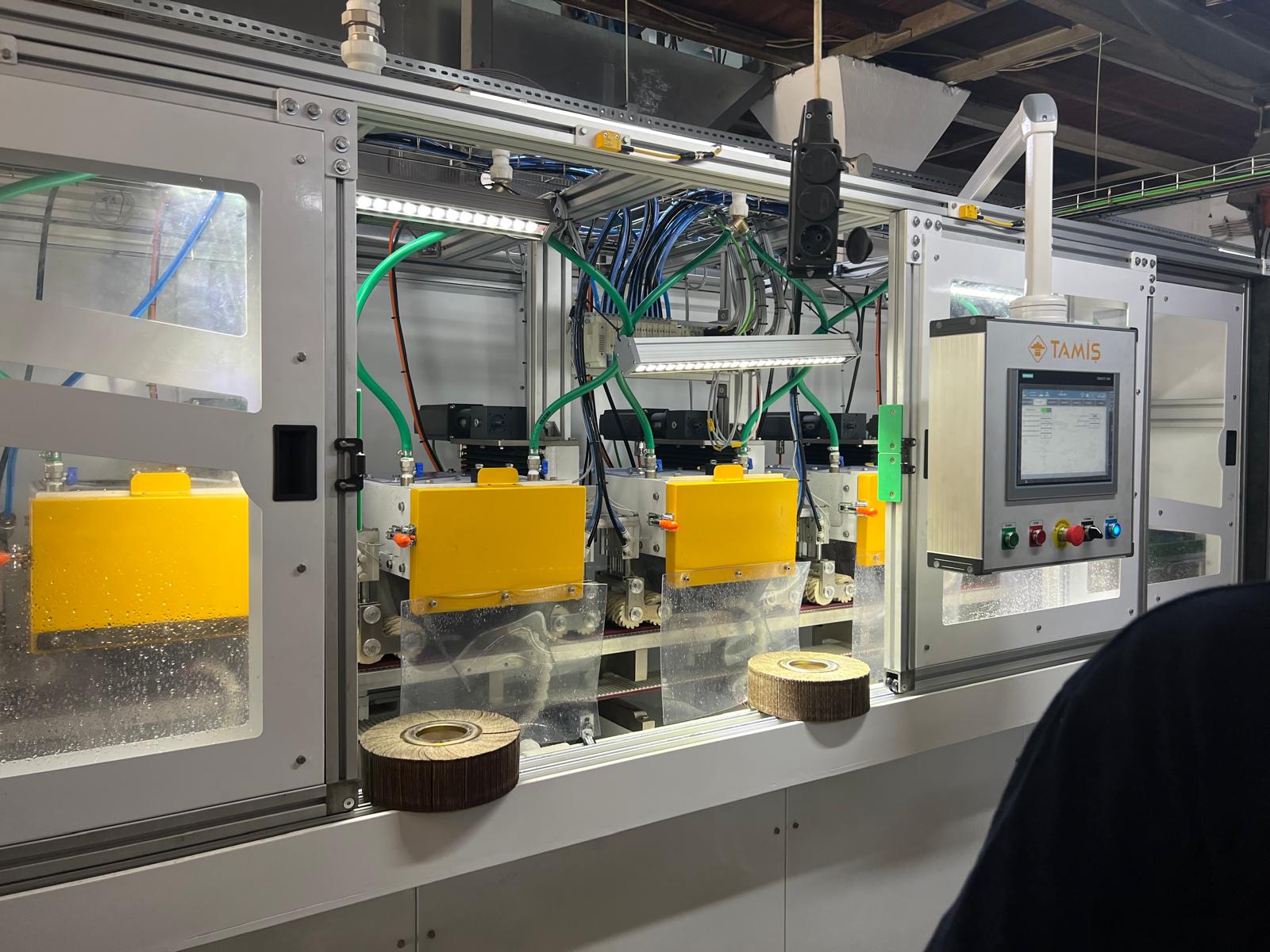
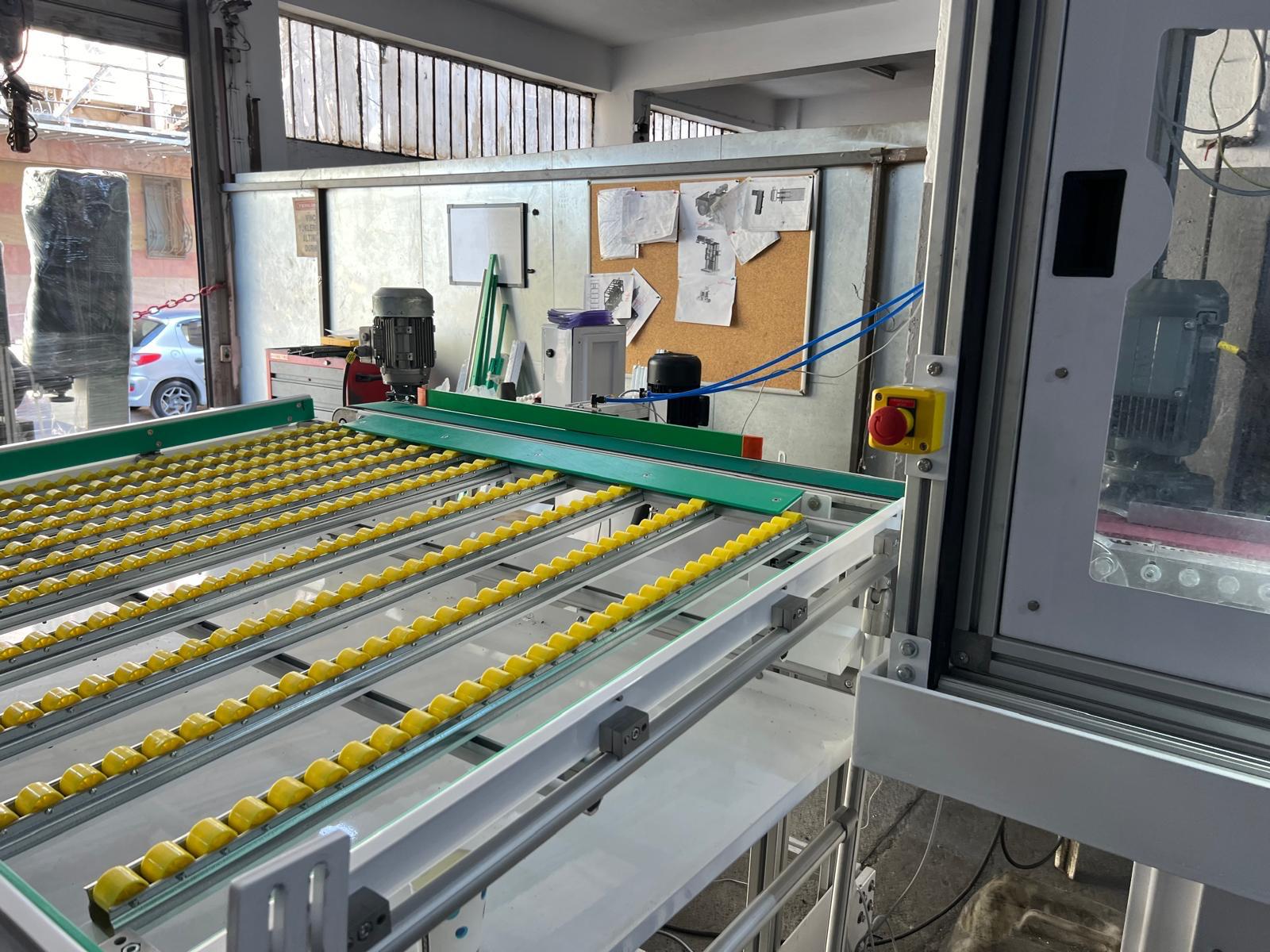
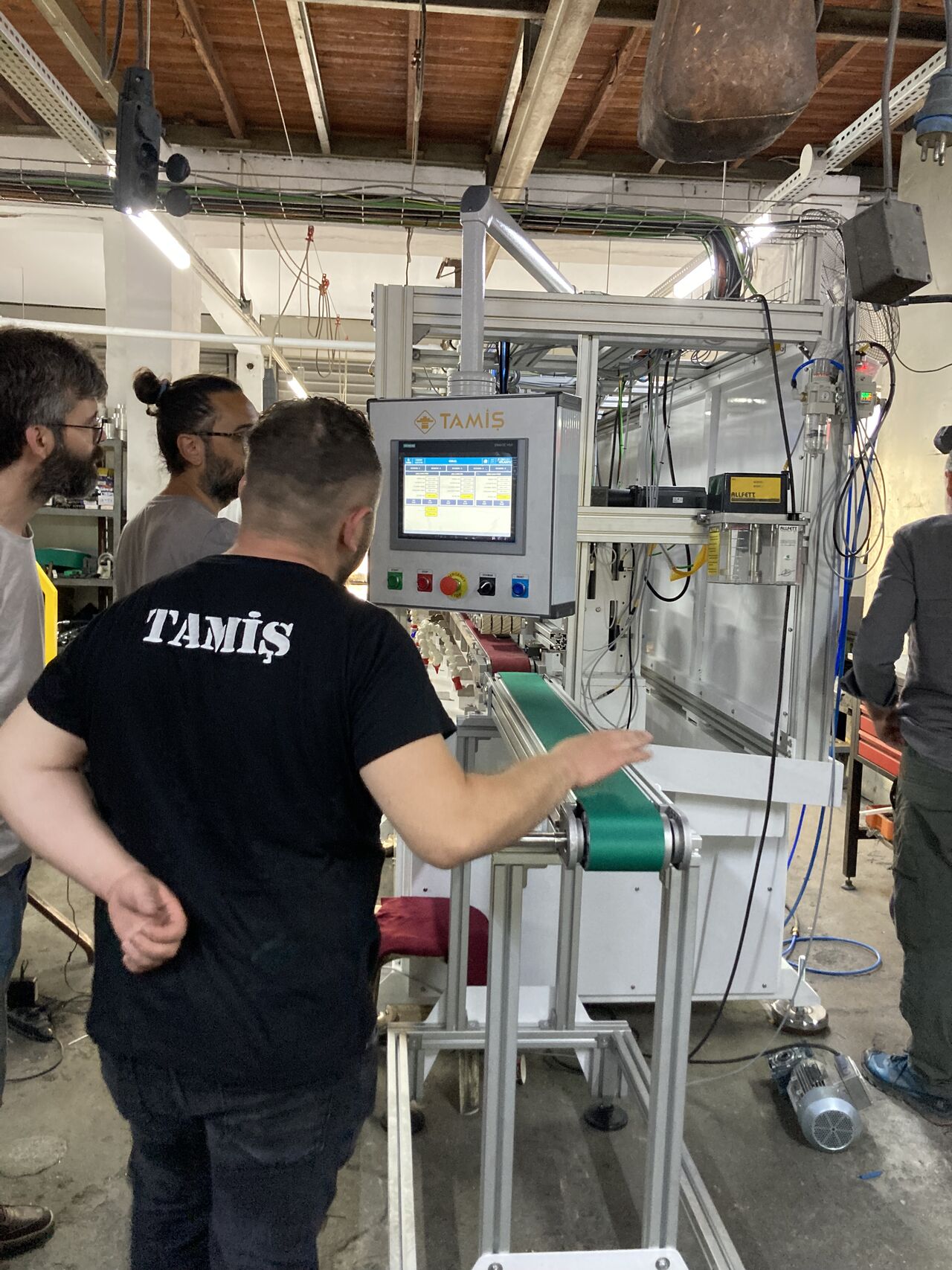
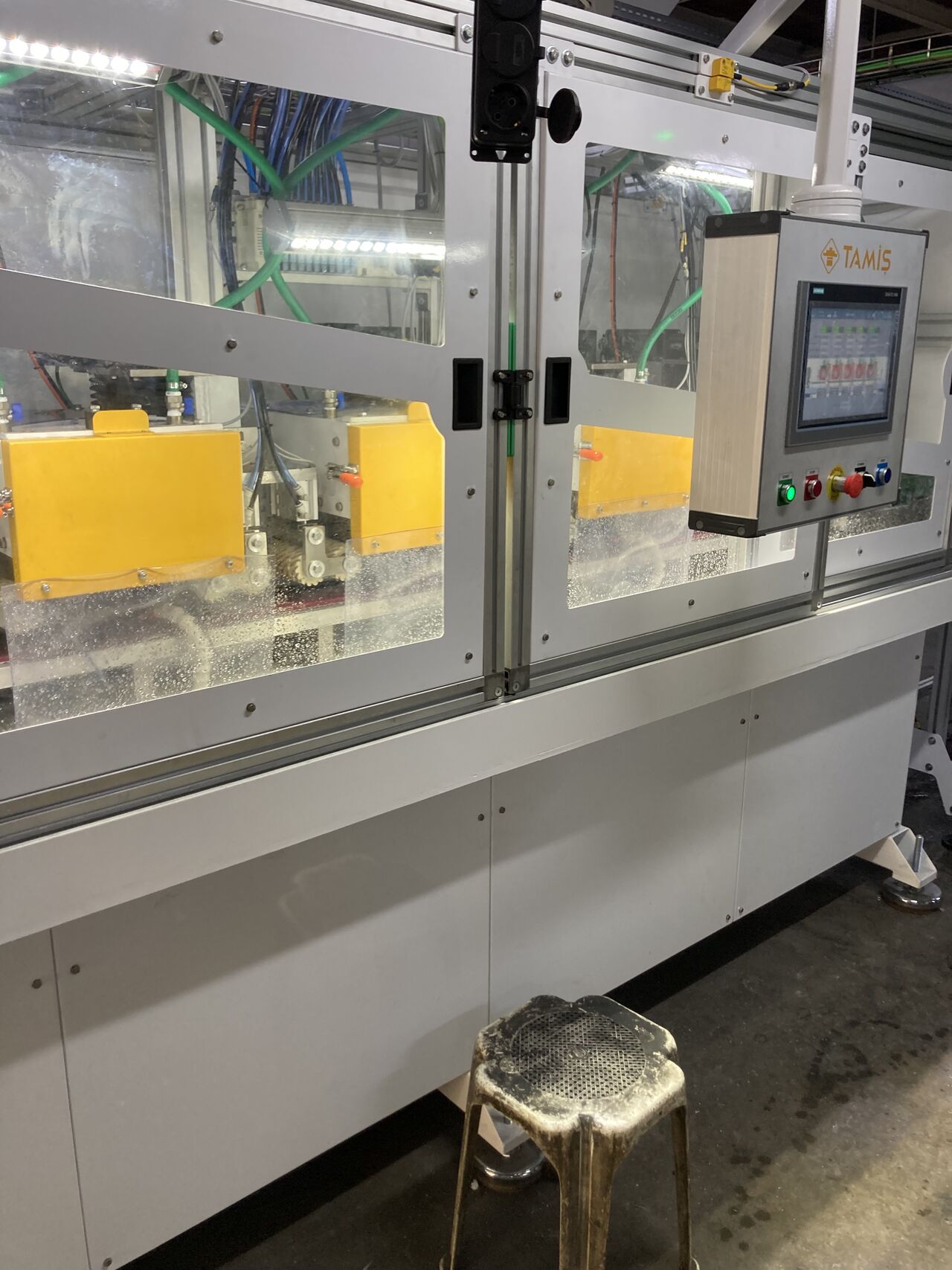
Tasarladığım Ana Bileşenler
- Infeed Konveyör (Giriş Sistemi): Operatör tarafından elle parçaların yerleştirildiği alan. Taşıma bantları ve rulolu sistem sayesinde, parçalar düzgün pozisyonla taşlama bölgesine alınır.
- Outfeed Konveyör (Çıkış Sistemi): İşlem görmüş parçaların taşlama ünitesinden sonra çıkışına rehberlik eder. Pnömatik silindir ve sensör sistemiyle entegre çalışır.
- Parça Toplama ve Yönlendirme Ünitesi: Zımparalama sonrası ürünler, sensör ile tetiklenen pnömatik piston vasıtasıyla parçaların yönlendirilmesini sağlar. Parçalar, alt kısımdaki havuza yönlendirilerek birikir.
- Manyetik Pencereler (Erişim ve Güvenlik): İş güvenliği kapsamında makinenin belirli bölgelerine yerleştirilen manyetik sensörlerle güvenlik alanı ve pencereleri tasarlandı. Kapaklardan biri açıldığında sistem otomatik olarak duracak şekilde güvenlik kontrolü entegre edildi.
Sorumluluklarım
- Tüm mekanik tasarım süreci (SolidWorks) tarafımdan yürütüldü: Giriş ve çıkış konveyörleri, sarı renkli taşıma-teker sistemi, kapatma ve bakım kapaklarının montaj geometrileri, otomasyonla uyumlu arayüzler.
- Malzeme seçimi, profil ve sac kalınlıkları, motor yerleşimleri ve pencere menteşe hatları dahil tüm detaylara karar verdim.
- İmalat planlaması, satın alma listeleri ve montaj yönlendirmeleri tarafımdan hazırlandı ve birebir sahada uygulandı.
Sistem İşleyişi ve Sonuçlar
- Sistem İşleyişi:
- Operatör, havlupanı giriş konveyörüne yerleştirir.
- Parça sensörle algılanır ve zımpara kafalarının bulunduğu bölgeye taşınır.
- Her bir zımpara kafası, sırayla işlemi gerçekleştirir.
- İşlem tamamlandıktan sonra parça, çıkış konveyörü üzerinden pnömatik pistonla aşağıdaki toplama havuzuna aktarılır.
- Tüm döngü boyunca kontrol, HMI panel üzerinden sağlanır.
- Sonuçlar:
- Otomasyon sayesinde işlem süresi manuel yöntemlere göre %60 daha kısa.
- Operatörle temas edilen nokta azaltılarak iş güvenliği riski düşürüldü.
- Dış kasada kullanılan manyetik kapaklar, bakım kolaylığı ve erişim güvenliği sağladı.
- Proje zamanında ve sıfır hata ile tamamlanarak devreye alındı.
Ahşap Beşik Parçaları İçin Finisaj Zımpara Makinesi
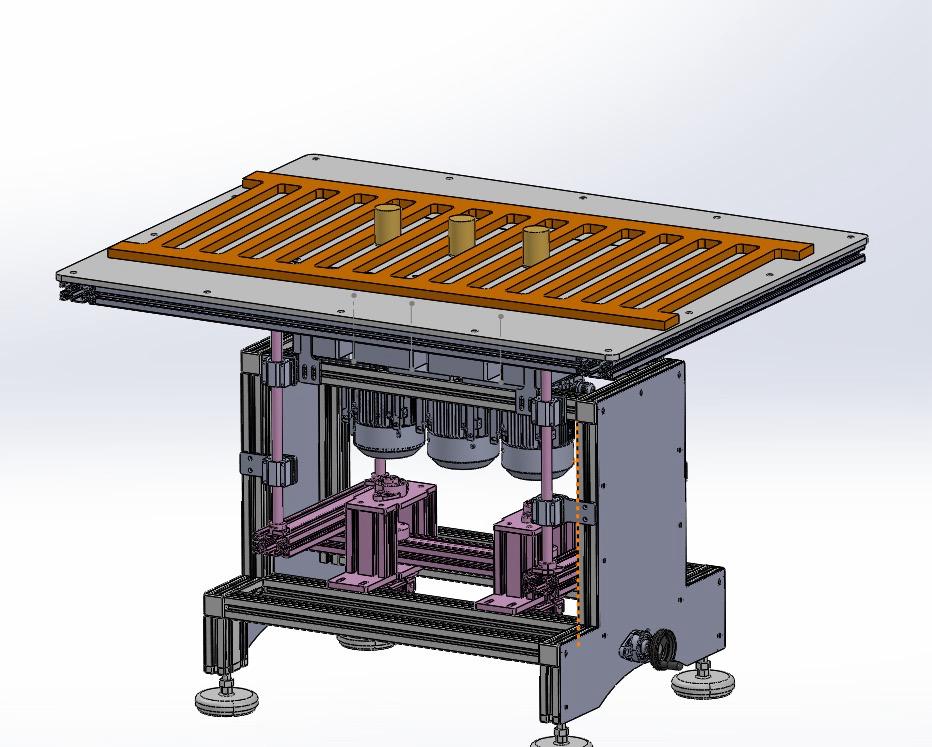
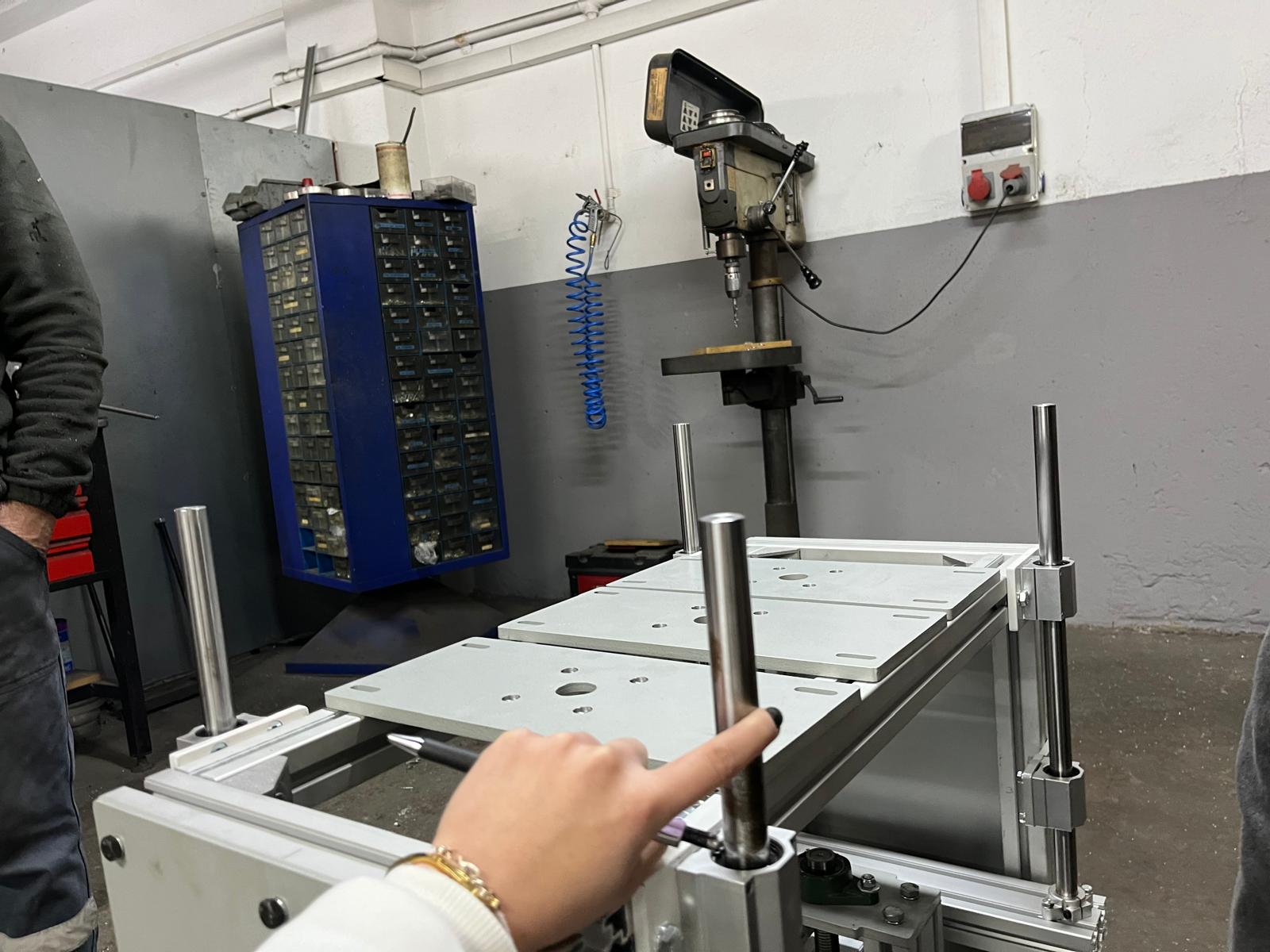
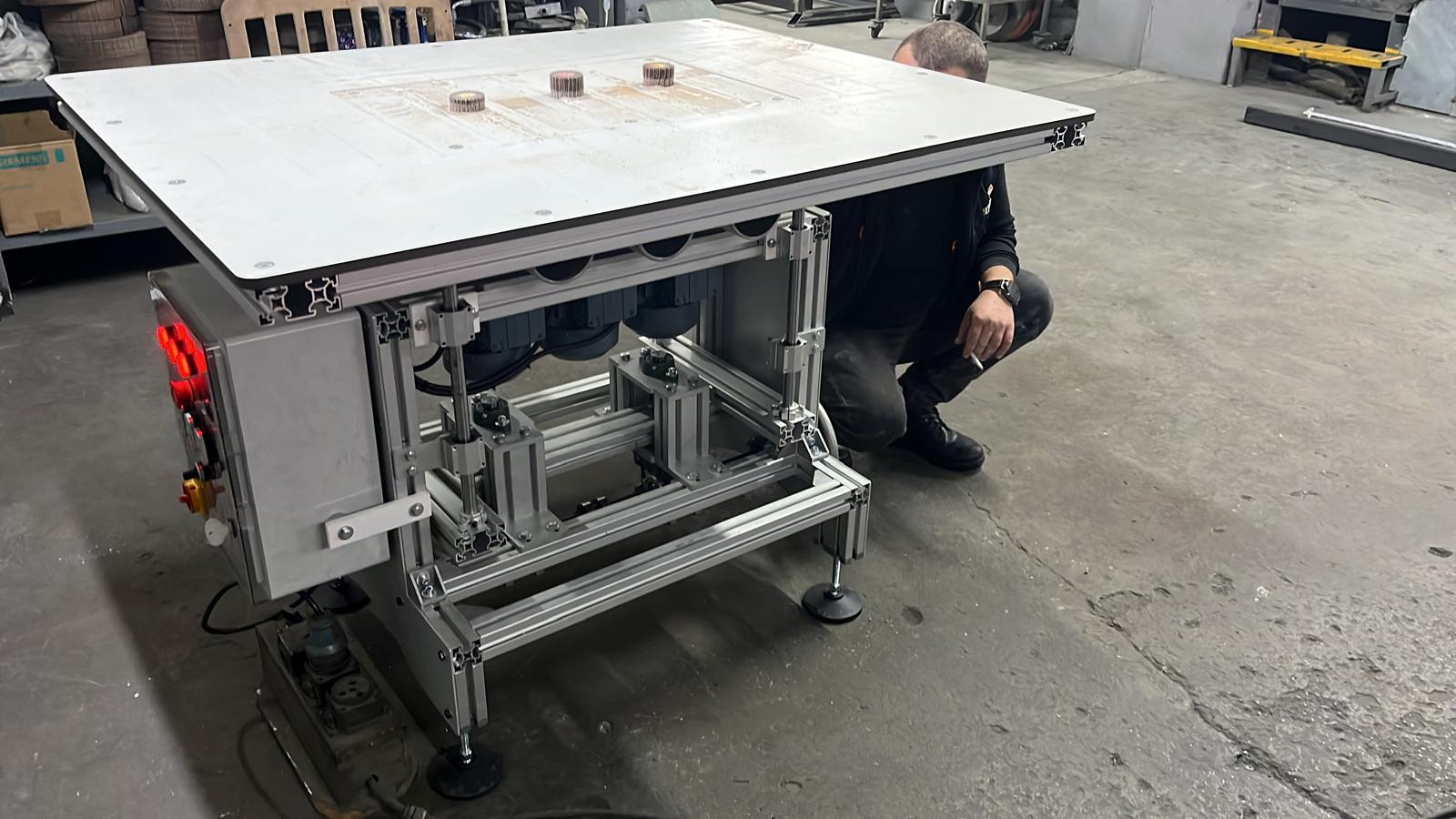
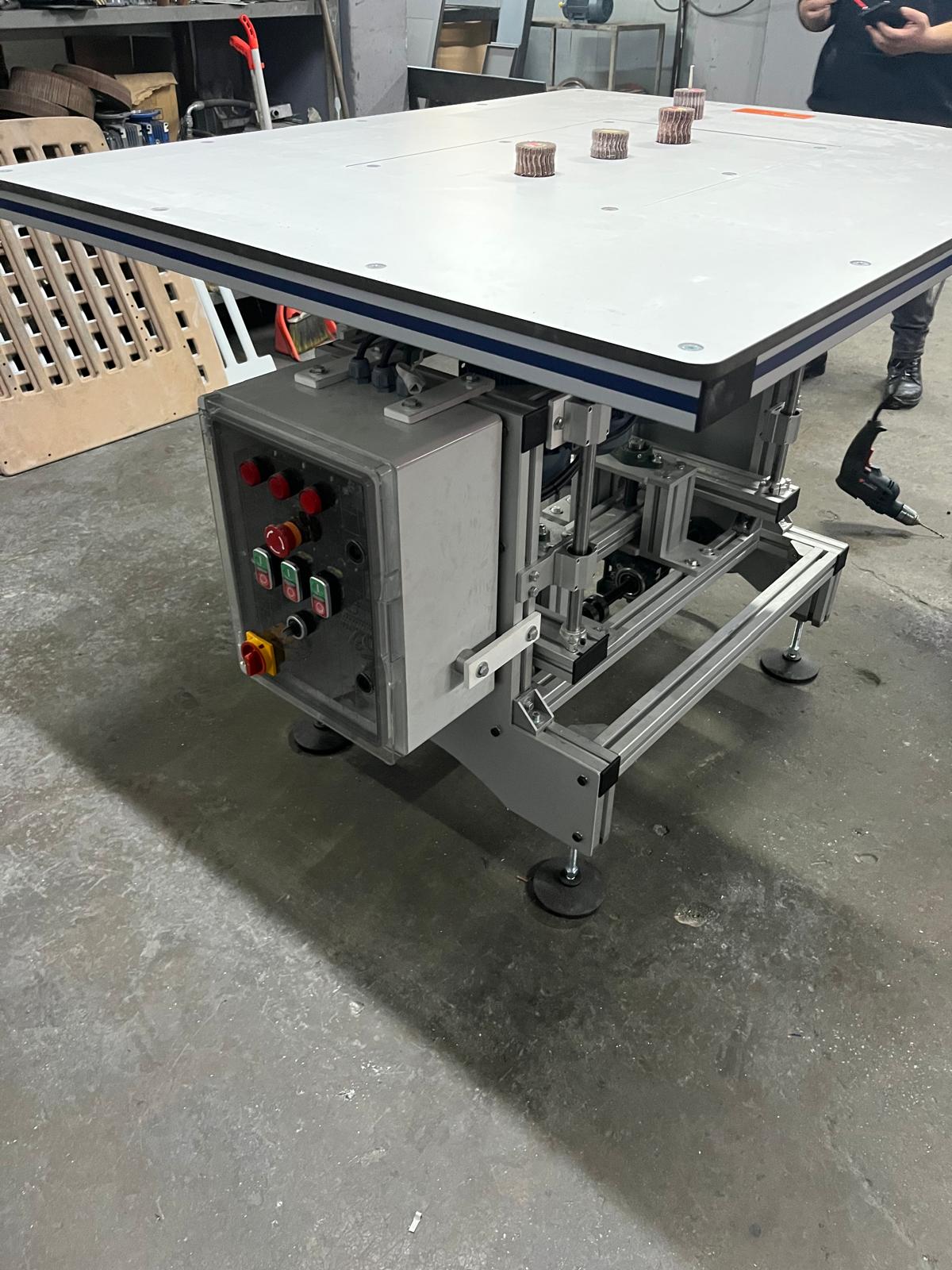
Teknik Özellikler
- Zımpara Konfigürasyonu: Dik olarak uzanan zımpara tamburu, üç ahşap parçayı tek seferde işleyebilecek uzunlukta konumlandırılmıştır. Slot içlerine erişimi kolaylaştırmak için özel açılı yerleşim planı uygulanmıştır.
- Masa Hareket Mekanizması: Zımpara motorları sabit tutulmuş, zımpara temasını sağlamak için yukarı-aşağı hareketli laminant masa tasarımı tercih edilmiştir. Bu hareket, alt kısımda bulunan kriko tipi vida mili sistemleri ile gerçekleştirilmiştir.
- Toz Toplama ve Koruma: Zımparalama sırasında açığa çıkan yoğun toz için motorların hemen üzerinde bir toz toplama bölgesi entegre edilmiştir. Aynı zamanda motor rulmanları, tozdan korunacak şekilde konumlandırılmıştır.
- Şasi ve Gövde Yapısı: Alüminyum profiller ve sac konstrüksiyonun birleşiminden oluşan modüler şasi, kolay bakım ve montaj imkanı sağlar. Tabla üzerinde vida karşılığı delik ve kanal geometrileri parça sabitleme için optimize edilmiştir.
Sorumluluklarım
- Makinenin tüm tasarımı, mekanik planlaması, malzeme seçimi ve imalat süreci şahsım tarafından yürütülmüştür.
- 3D modelleme ve montaj simülasyonları SolidWorks üzerinde hazırlanmış; çizimler sahaya doğrudan aktarılmıştır.
- Vida milinin dönüşü ile birlikte düzgün yükselme sağlanacak şekilde lineer kızak geometrileri ve yataklama sistemleri planlanmıştır.
- Kullanıcı panelleri, acil durdurma ve kontrol sistemi tarafımdan yerleştirilmiş, sistemde tek operatörle çalışabilirlik sağlanmıştır.
Çıktılar ve Katma Değer
- Boya öncesi ahşap temizliği manuel yöntemlere göre çok daha tutarlı ve zaman kazandırıcı hale gelmiştir.
- Slot bölgelerinin düzgün zımparalanması sayesinde boya kalitesi artmış, hatalı üretim oranı düşmüştür.
- Masa hareket sisteminin yukarıdan baskı yerine alttan kontrollü yükselme ile sağlanması, titreşimi azaltmış ve işlem hassasiyetini yükseltmiştir.
Kauçuk Kaplı Kasnak Tasarımı ve Kalıp Optimizasyonu (AR-GE Süreci)
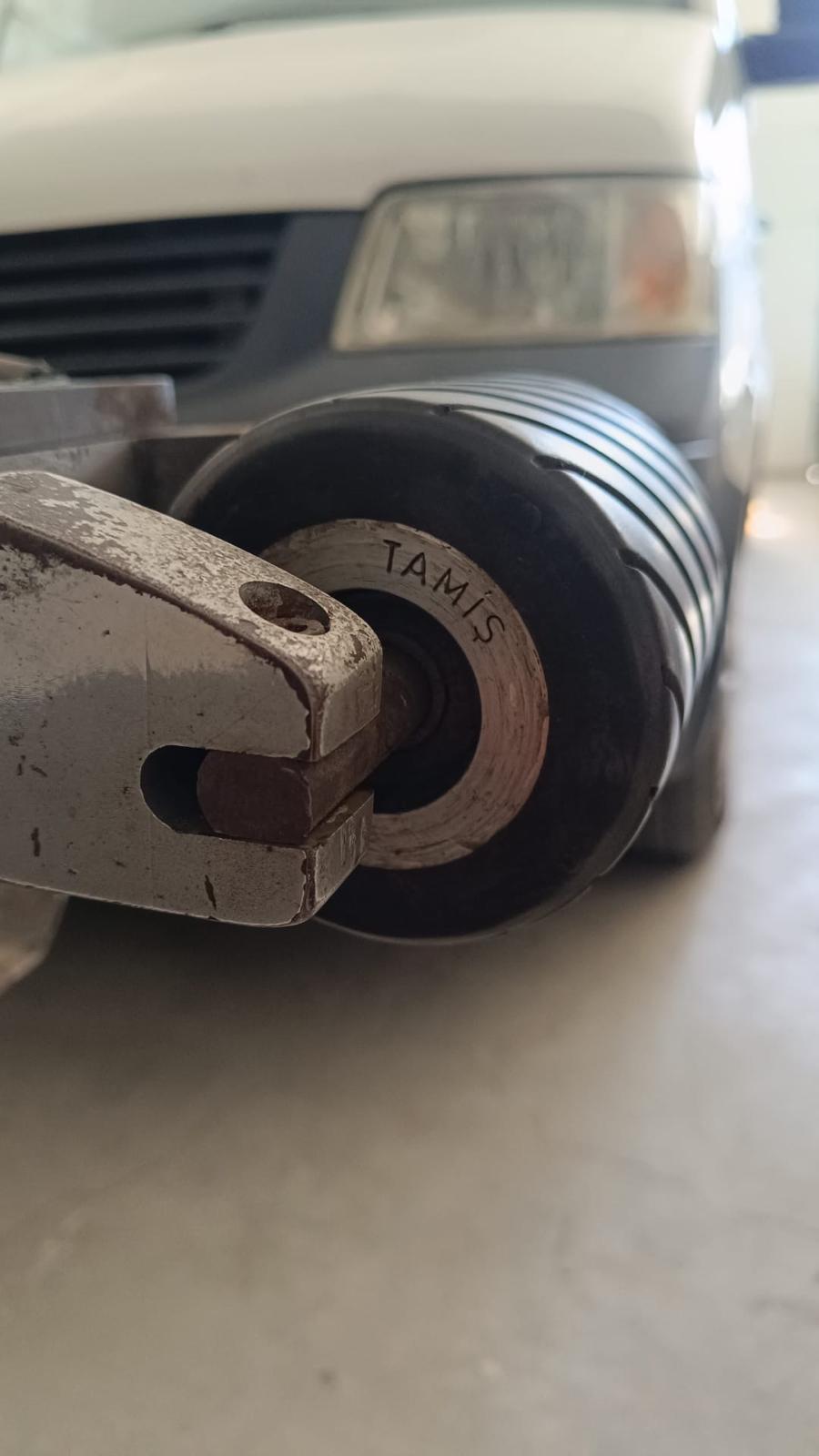
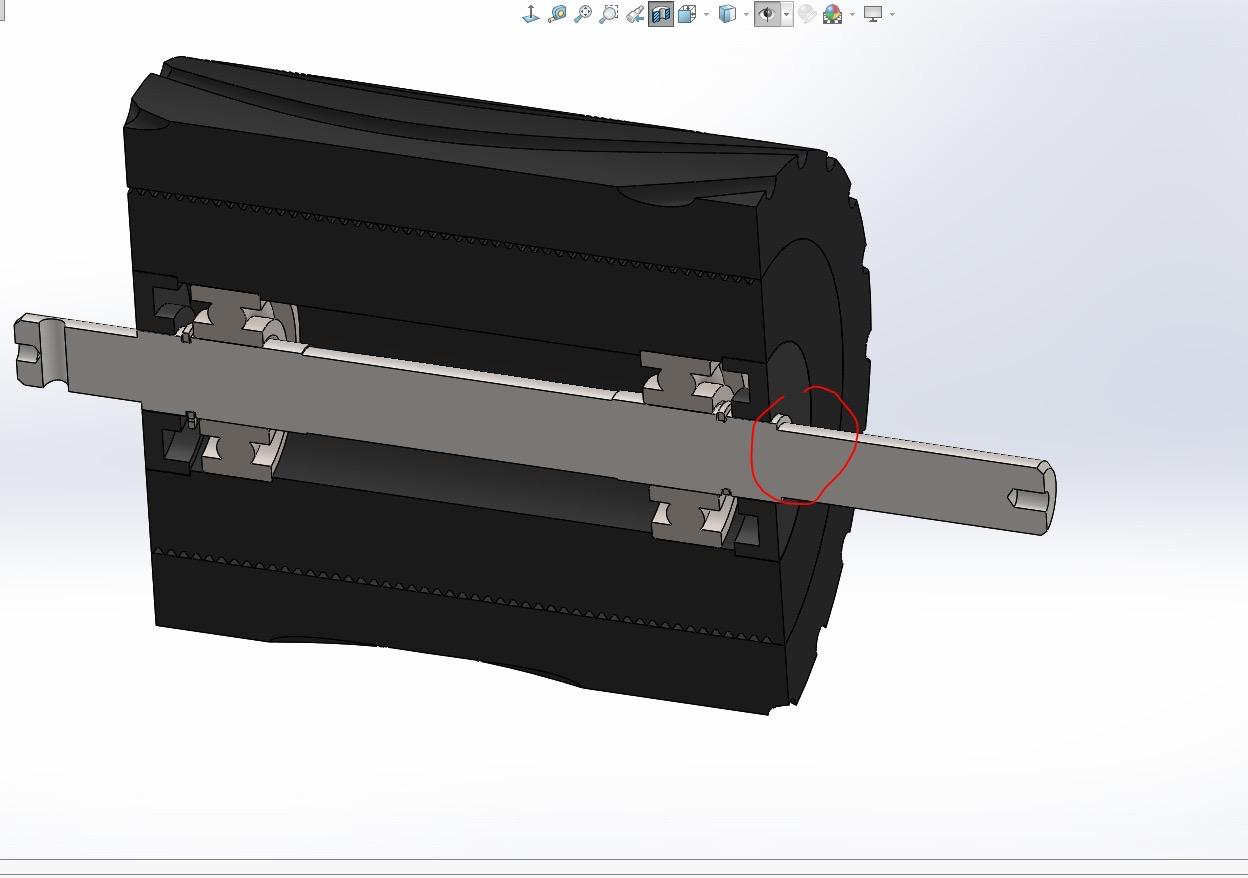
Teknik Süreç ve Tasarım Aşamaları
- Kauçuk Form Geometrisi Optimizasyonu: Kauçuk yüzeyde yer alan oluklar ve tümsek yapıları, kalıptan rahat çıkacak, ancak performanstan ödün vermeyecek şekilde yeniden boyutlandırıldı. SolidWorks üzerinde parametrik modellerle farklı varyasyonlar denendi, optimum profil elde edildi.
- Kalıptan Çıkma Analizi: SolidWorks’ün Tooling (Kalıp Modülü) kullanılarak kalıbın açılma yönü, parçanın kalıptan çıkarken deformasyona uğrayıp uğramayacağı analiz edildi. Bozulma riski olan geometriler yeniden düzenlenerek yırtılma ve yapışma problemi ortadan kaldırıldı.
- Numune Üretimi ve Performans Testleri: Yeni form üzerinden kalıp çizimleri hazırlanarak üretici firmaya gönderildi. Üretilen kalıp ile bir adet kauçuk numune kasnak döküldü ve test amaçlı makineye montajı yapıldı.
Test ve Sonuçlar
- Titreşim ve dengesizlik testi: Yalpa, atalet dengesizliği ve eksantriklik gözlemlenmedi.
- Gürültü testi: Desibel cihazı ile ölçülen ses seviyesi, iş sağlığı ve güvenliği standartlarına uygun bulundu.
- Yüzey sertliği ve dayanım: Kullanıcı geri bildirimlerine göre yeni form, önceki versiyonlara göre daha dengeli ve kullanıcı dostu bulundu.
Katkılarım
- Problemin tanımı ve çözüm senaryosu geliştirme
- 3D modelleme, oluk geometrisi optimizasyonu ve analiz süreci
- Kalıp tasarım çizimlerinin hazırlanması ve üretici firma ile teknik iletişim
- Numune test sürecinin sahada yürütülmesi, titreşim ve ses ölçümlerinin gerçekleştirilmesi
Bu proje, yalnızca görsel ve işlevsel değil, aynı zamanda fonksiyonellik–imalat kolaylığı dengesini yakalayan bir AR-GE çalışmasıdır. Endüstriyel gürültü, titreşim ve bakım kolaylığı gibi etkenlerin tasarıma etkisi göz önüne alınmıştır.
Dikey ve Yatay Konfigürasyonlu Bantlı Zımpara Makineleri
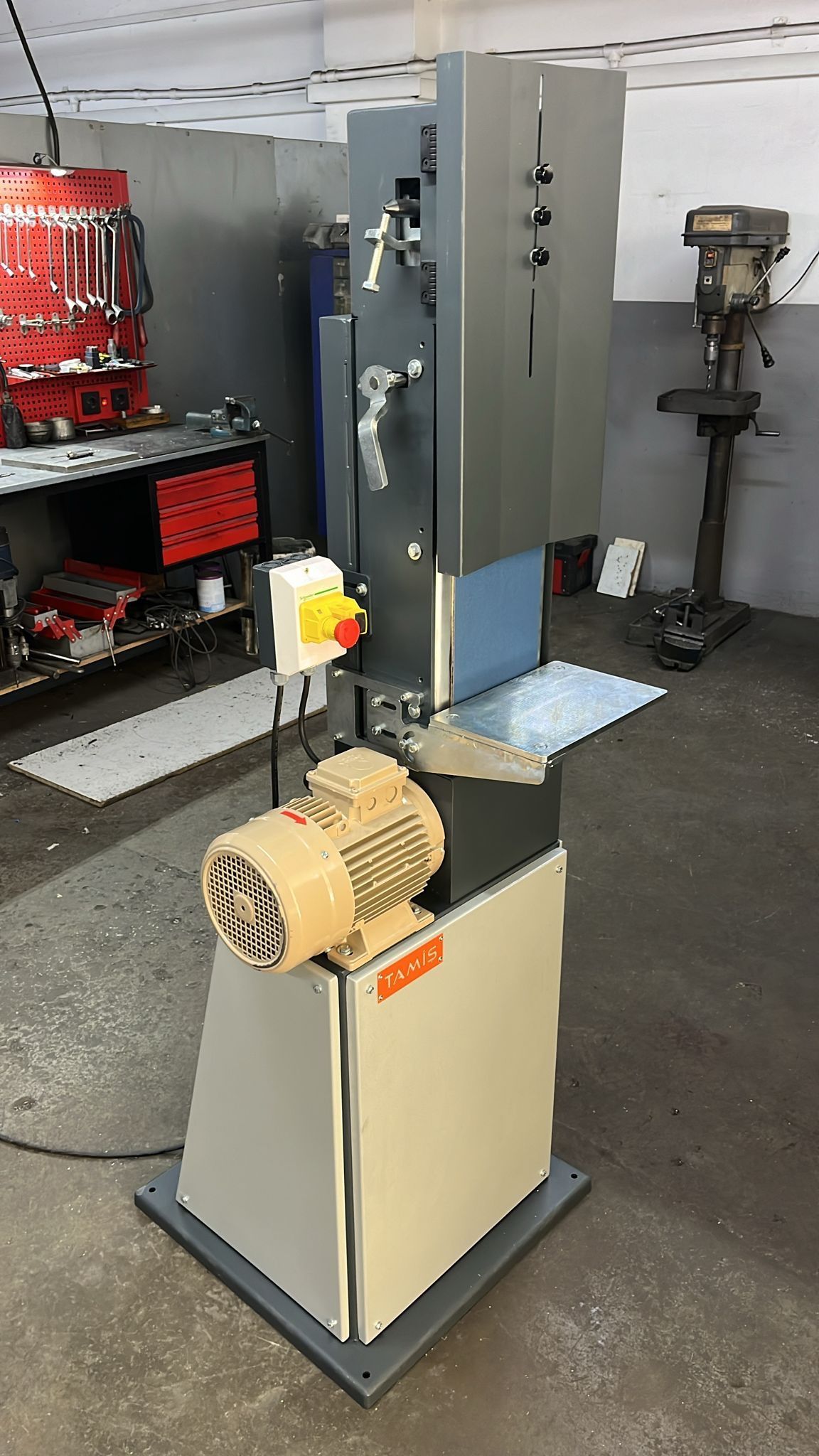
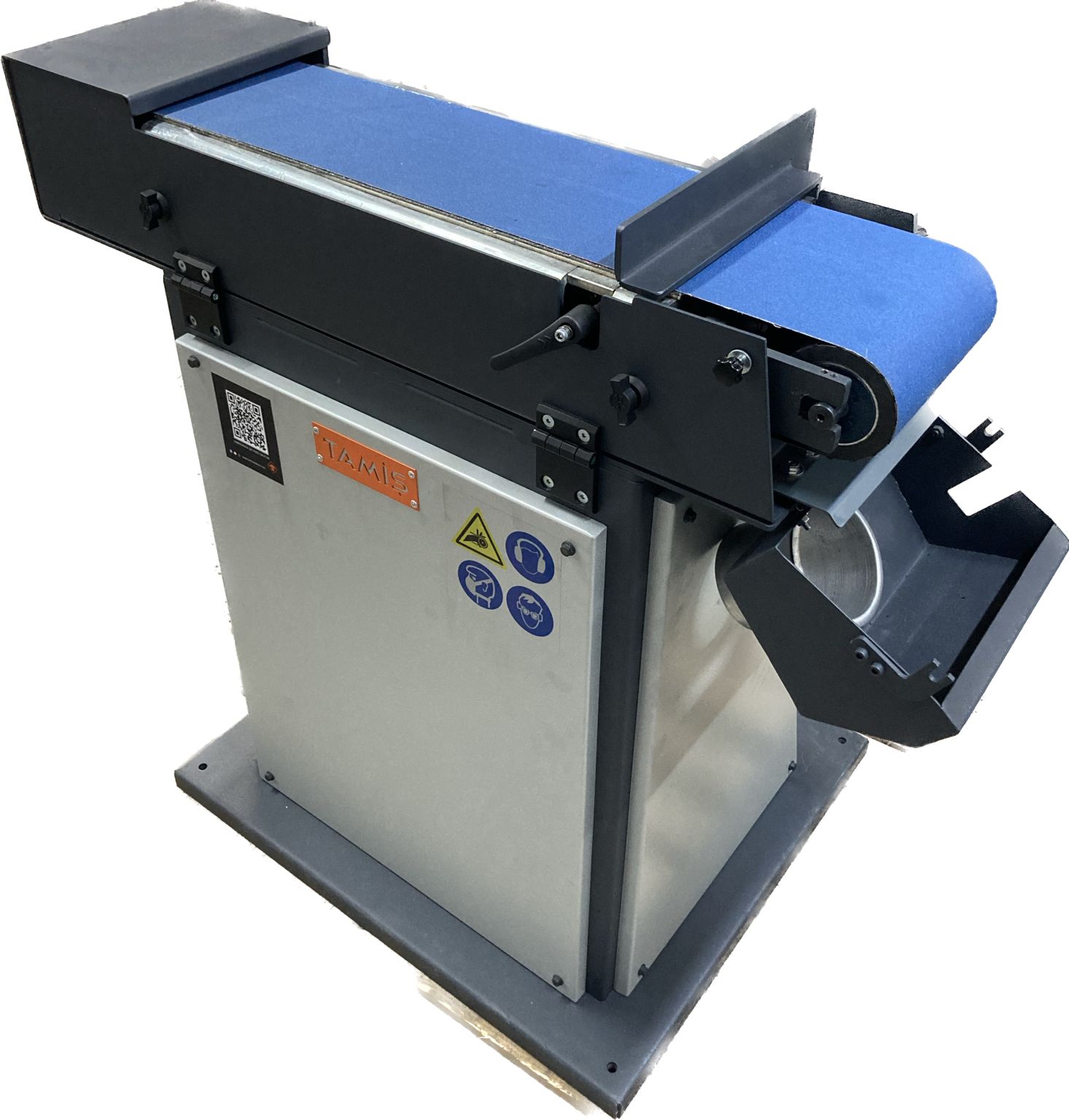
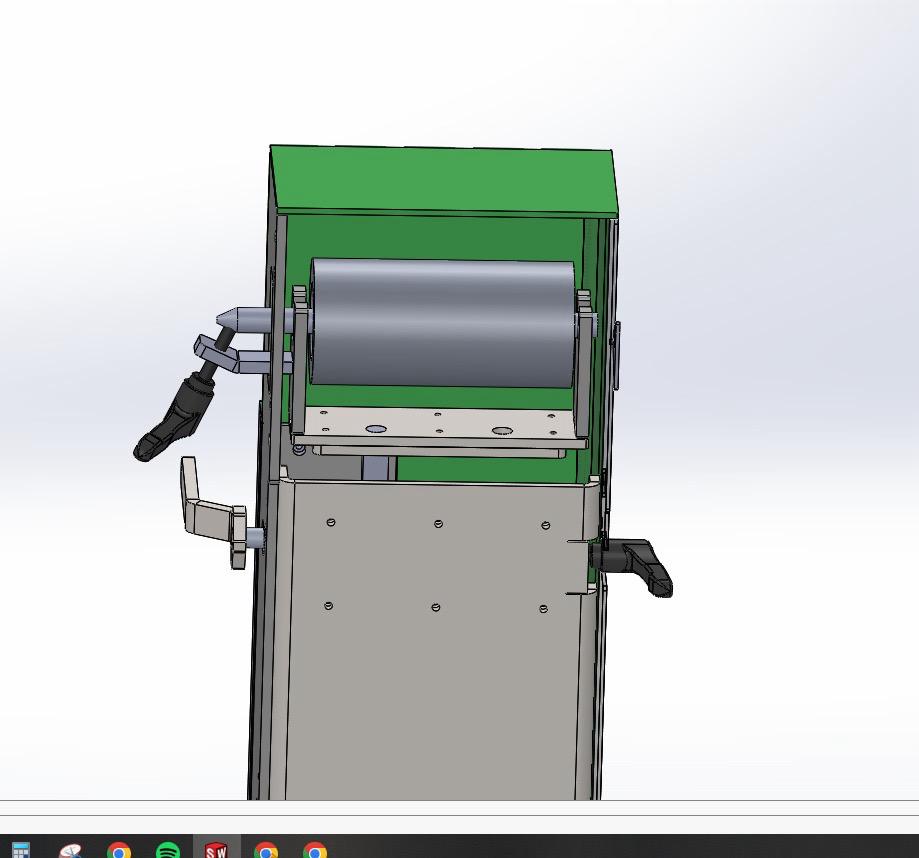
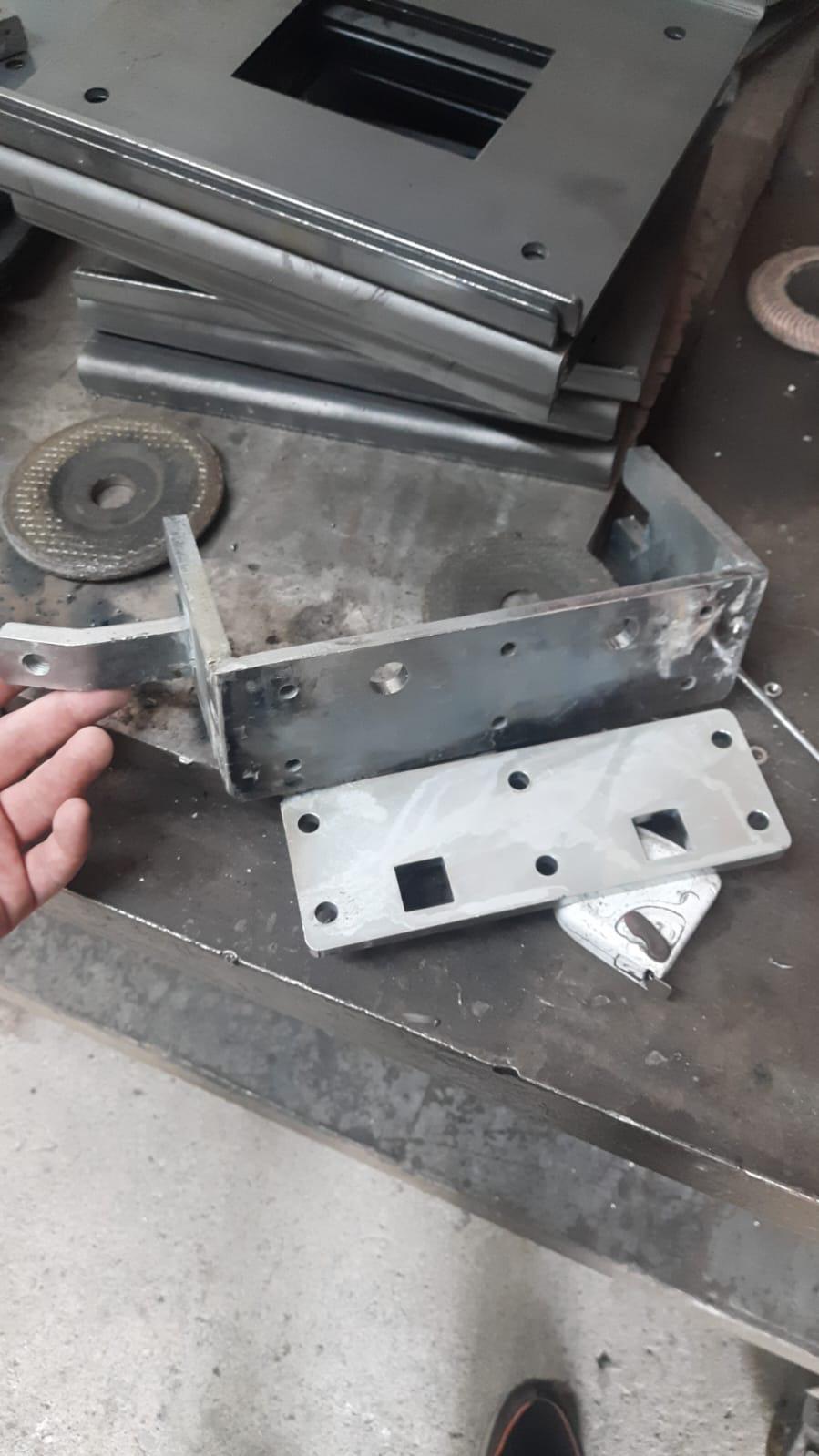
Teknik Geliştirmeler ve Revizyonlar
- Genel Yapısal Revizyonlar: Tüm sistemin gövdesi yeniden CAD ortamında modellenerek estetik, erişilebilirlik ve üretim kolaylığı açısından sadeleştirilmiş yapıya kavuşturuldu. Taban sacı kalınlaştırılarak titreşim emilimi artırıldı.
- Mekanik Parça Güncellemeleri: Önceki versiyonda bulunan röle yerleşimleri, tabla sabitlemeleri ve krameyer parçalar, hem işlevsellik hem de montaj kolaylığı açısından iyileştirilmeler yapıldı. Tabla sabitliği ve kullanıcı ayar hassasiyeti artırıldı.
- Tahrik ve Aktarma Elemanları: Kayış gerginlik mekanizmaları, ayarlanabilir ve tekrar kullanılabilir yapıda optimize edildi. Krameyer yuvalarında kolay kaynak yapılması açısından tasarım iyileştirildi ve zımparanın gergi mekanizması için tek krameyer den iki krameyere geçildi.
Tasarım Süreci ve Üretim Sonuçları
- SolidWorks üzerinden yürütülen modelleme çalışmaları sonucunda hem yatay hem de dikey varyant için üretim çizimleri hazırlandı.
- Her iki modelin de en son teknik çizimleri arşive kazandırıldı ve bu sayede şirket içinde seri üretim süreci başlatıldı.
- Operatörle yapılan geribildirim görüşmeleriyle, kullanıcı dostu tabla boyutları, kumanda kol yerleşimi ve bant yönü optimize edildi.
Kazanımlar ve Etkiler
- Önceki versiyonlara göre:
- Ses seviyesi yaklaşık %30 azaldı
- Bakım süresi ve motor sökme/germe işlemleri %40 kısaldı
- Zımpara bandı değişim süresi ortalama 2 dakikaya indirildi.
- Makine artık tek operatör tarafından hızlıca kurulum ve kullanım sağlayacak şekilde tasarlanmış durumda.
- Dikey model, dar atölye ortamlarında yerden tasarruf sağlamaktadır; yatay model ise geniş tabla sayesinde büyük parçalarda daha verimli çalışmaktadır.
Destekleyici Teknik Görevler ve Proje Dışı Sorumluluklar
Makine tasarımı ve üretim süreçlerine doğrudan katkı sağlayan projelerin dışında, hem kişiye özel hem de seri üretim makinelerin sürdürülebilirliği, güvenliği ve operasyonel yönetimi konusunda aktif roller üstlendim.
1. Güvenlik ve Giydirme Mekanizmalarının Tasarımı
- Farklı ebat ve özellikteki makineler için, operatör güvenliğini artıran özel sac kabinler, koruma muhafazaları ve erişim kapakları tasarlandı.
- CE standartlarına uygun etiketleme, ikaz ikonları ve kapatma sistemleri entegre edildi.
- Giydirme tasarımları, estetik değil; ergonomi ve bakım kolaylığı da sağlayacak şekilde planlandı.
2. Yedek Parça Tasarımı ve Listelendirme Süreçleri
- Her projeye ait yedek parça tanımlamaları yapıldı; hem sistem bileşenleri hem de sarf malzeme sınıfında takip sistematiği oluşturuldu.
- Tüm yedek parçalar için montaj konumu, teknik özellik ve kullanım amacı gibi detayları içeren listeler hazırlandı.
- Kritik parçalar için olası revizyon durumlarında güncel teknik dokümantasyon üretildi.
3. Fiyat Alma ve Sipariş Yönetimi
- İmalat için gerekli komponentler ve alt parçalarla ilgili olarak tedarikçi araştırmaları, fiyat karşılaştırmaları ve teknik uyum kontrolleri tarafımdan yapıldı.
- Alternatif tedarik kaynaklarının teknik yeterlilikleri incelenerek satın alım süreci desteklendi.
- Sipariş takibi ve parça uygunluk kontrolü üretim sürecine entegre şekilde yürütüldü.
4. ERP Sistemi Üzerinden Teknik Veri Girişi (Netsis)
- Parça ve ürün grubu için ürün fişi (malzeme ağaçları) Netsis sistemine tarafımdan girildi.
- Ürün–parça eşleştirme, satın alma kodu, teknik açıklamalar ve stok grupları eksiksiz şekilde tanımlandı.
- ERP üzerinden yedek parça hareketleri, üretim ilişkileri ve ihtiyaç planlaması kontrol altına alındı.
Sonuç
Bu görevlerle birlikte:
- Tüm makineler üretim sonrası bakım ve yedek parça yönetimine hazır hale getirildi,
- Firma içi satın alma süreçleri teknik destekle hızlandırıldı,
- Ürün dokümantasyonu tek merkezde güncel ve izlenebilir kılındı,
- Teknik veri sürekliliği sağlanarak hem mühendislik hem de üretim tarafında verimlilik artırıldı.
Bitirme Projesi: Investigation of Air Intake Design of a Fighter Jet
Proje Özeti
Bu bitirme projesi, bir savaş uçağı için jet motoru hava alığı tasarımının performansını teorik ve sayısal yöntemlerle araştırmayı amaçlamıştır. Özellikle askeri uygulamalarda kullanılan S-şekilli hava alıkları (S-duct) odak alınmış, farklı hücum açılarındaki aerodinamik davranışları analiz edilmiştir.
Teknik İçerik ve Yöntem
- Temel Parametreler:
- Mass Flow Rate
- Pressure Recovery Coefficient (PR)
- Distortion Coefficient (DC)
Bu üç temel performans kriteriyle hava girişi verimliliği değerlendirildi.
- Sayısal Simülasyonlar:
- ANSYS Fluent kullanılarak S-duct geometrileri üzerinde farklı açılarda (0°, 5°, 10°) CFD (Computational Fluid Dynamics) analizleri gerçekleştirildi.
- RAE M2129 S-diffuser modeli üzerinden validasyon çalışmaları yürütüldü.
- Ağ (Mesh) Yapısı ve Doğrulama:
- Yüksek kaliteli ağ yapısı üretildi (skewness, orthogonallik analizleri yapıldı).
- AGARD DP 3532 ve DP78 gibi literatürde yer alan verilerle karşılaştırmalı validasyon yapıldı.
- Performans Sonuçları:
- PR (Pressure Recovery) değerinin hücum açısı arttıkça azaldığı tespit edildi.
- Düşük açılarda giriş performansı daha yüksek çıktı.
- DC’nin belirli bölgelerde motor performansını olumsuz etkileyebileceği belirlendi.
Kullanılan Araçlar ve Yaklaşımlar
- Yazılım: SolidWorks (taslak geometriler), ANSYS Fluent
- Yöntem: Yüzey ağı (meshing), simetri düzlemi üzerinden hız/akış alanı analizi, AIP (Aerodynamic Interface Plane) üzerine verilerin aktarımı
- Karşılaştırmalı Çalışmalar: AGARD, RAE, NASA doğrulama verileriyle
Kazanımlar ve Proje Katkısı
- Jet motoru hava alıklarının tasarımına dair derinlemesine bir mühendislik yaklaşımı kazanıldı.
- Sayısal analiz yoluyla giriş geometrisinin performansa etkisi incelendi.
Bu proje, ileride ikincil akış optimizasyonu ve tam aerodinamik modelleme için ön hazırlık teşkil etmektedir.
Proje Sunumu için Tıklayın